The risk-based inspection (RBI) approach is currently well established and widely used in the Oil & Gas, Refining, Petrochemical and Chemical Industries. The risk assessment, including consequence of failure and likelihood of failure, ranks items according to risk and allows elaboration of an effective inspection plan, including inspection methods, timing, and coverage. This is translated into a detailed inspection plan, which is executed, and the results are evaluated and fed back into the next cycle of risk assessment and inspection planning. In addition to inspection, other mitigation measures may need to be taken if the risk is still high or if the inspection identifies specific issues.
The RBI application benefits
The RBI application benefits are well known, and they are summarized by API RP 580 (2016):
⦁ RBI facilitates the development of optimised plans (inspection or mitigation plans) to manage risks on an equipment level
⦁ RBI may provide an overall reduction in risk for the facilities and equipment assessed
⦁ RBI provides an acceptance/understanding of the current risk
⦁ RBI may identify equipment items that do not require inspection or some other form of mitigation. Inspection & maintenance activities can be focused and more cost effective. This results in a significant reduction in the amount of inspection data that is collected. RBI inspection plans may also result in cost reductions.
The RBI Process
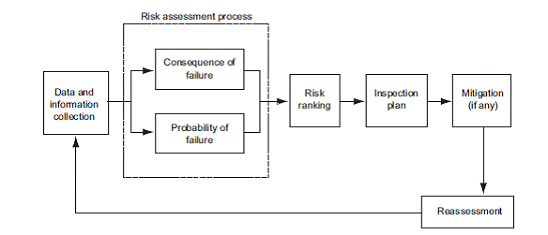
Results
The analysis helps in planning the inspection activities for the periodic turnaround / shutdown as well as for planning the on-stream inspections. Since many plant inspections are still performed during the shutdowns, this approach is typically appropriate for defining the scope of inspections for the shutdown.
⦁ Written Scheme of Examination
A written scheme of examination is a document containing information about selected items of plant or equipment which form a pressure system, operate under pressure, and contain a ‘relevant fluid’.
CONTENTS OF WSE
Typical contents of a written scheme of examination include:
⦁ Identification of the items of plant or equipment within the system.
⦁ Those parts of the system which are to be examined.
⦁ The nature of the examination required, including the inspection, and testing to be carried out on any protective devices.
⦁ The preparatory work needed for the item to be examined safely.
⦁ Where appropriate, the nature of any examination needed before the system is first used.
⦁ The maximum interval between examinations.
⦁ The critical parts of the system which, if modified or repaired, should be examined by a competent person before the system is used again.
⦁ The name of the competent person certifying the written scheme of examination; and
⦁ The date of certification.
DRAWING THE WSE
⦁ Identify which items of plant or equipment operate under pressure and form a pressure system.
⦁ follow the steps described in the chart below
⦁ check the exceptions to the Regulations, as you may find your pressure system does not require a written scheme of examination at all
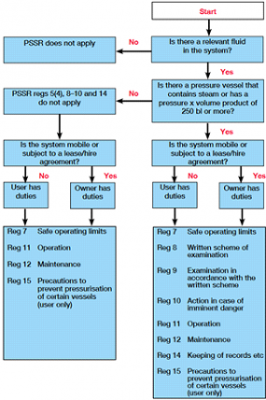
Sstems that require a SWE
The following pressurised systems are likely to require a written scheme of examination:
⦁ Compressed air receiver and the associated pipework, where the product of the pressure in bars multiplied by the internal capacity in litres of the receiver is equal to or greater than 250 bar litres.
⦁ Steam sterilising autoclave and associated pipework and protective devices.
⦁ Steam boiler and associated pipework and protective devices.
⦁ Gas-loaded hydraulic accumulator.
⦁ The components of self-contained breathing apparatus sets (excluding the gas container).
⦁ Fixed liquefied petroleum gas (LPG) storage system, supplying fuel for heating in a workplace.