Plant layout is a mechanism which involves knowledge of the space requirements for the facilities and involves their proper arrangement so that continuous and steady movement of the production cycle takes place.
Plant layout embraces the physical arrangement of industrial facilities. This arrangement, either installed or in plan, includes the space needed for material movement, storage, indirect labour and all other supporting activities or services, as well as for office equipment and personnel.
Plant layout is often a compromise between a number of factors, including safety aspects such as
⦁ The geographical limitations of the site.
⦁ The distances for transfer of materials between plant and storage units to reduce costs and risks.
⦁ Interaction with existing or planned facilities on site such as existing roadways, drainage, and utilities routings.
⦁ The spaces for plant operability and maintainability.
⦁ The hazardous and flammable material storages.
⦁ Emergency services and escape routes for on-site personnel.
⦁ The need to provide acceptable working conditions for operators.
⦁ Preventing and/or mitigating the escalation of adjacent events (domino effect).
⦁ Ensure that safety within on-site and off-site occupied buildings is maintained.
⦁ Controlling the access of unauthorised personnel.
Importance of Layout safety Review
Hazard assessment of site layout is critical to minimise consequences of loss of containment and chances of escalation. The Domino effect may be by fire, explosion or toxic gas cloud causing loss of control of operations in another location.
The spread of fire from its origin to other parts of the premises can be prevented by vertical and horizontal compartments using fire-resisting walls and floors. Consideration should also be given to the spread of flammable material via drains, ducts and ventilation systems. Delayed ignition following a release may result in the spread of flames.
Protection against domino effects by convection, conduction and radiation can be achieved by inherent safety principles, that is, ensuring that the distances between plant items are sufficient to prevent overheating of adjacent plants, therefore compromising the safety of those plants. Where this is not possible due to other restrictions, other methods, such as fire walls and active or passive fire protection, may be considered.
Plant Layout design techniques applicable to the reduction of the risks from release of flammable or toxic materials include:
⦁ Locating the storage of flammable/toxic material outside process areas.
⦁ Locating hazardous plants away from main roadways through the site.
⦁ Fitting remote-actuated isolation valves where high inventories of hazardous materials may be released into vulnerable areas.
⦁ Allowing for the provision of dykes and sloping terrain to contain releases, increase the safety and reduce environmental effects.
⦁ Siting of plants within buildings as secondary containment.
⦁ Siting of plants in an open-air environment to ensure rapid dispersion of minor releases of flammable gases and vapours and thus prevent concentration build-up which may lead to flash fires and explosions.
⦁ Hazardous area classification for flammable gases, vapours and dusts to designate areas where ignition sources should be eliminated.
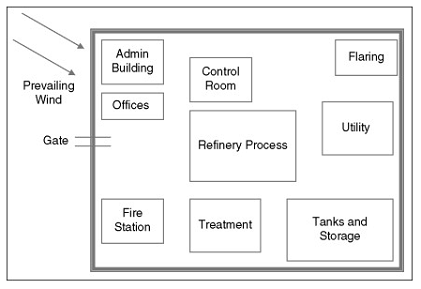
The distance between occupied buildings and plant buildings will be governed by the need to reduce the dangers of explosion, fire, and toxicity. Evacuation routes should not be blocked by poor plant layout, and personnel with more general site responsibilities should be housed in buildings sited in a non-hazard area near the main entrance. Consideration should be given to the siting of occupied buildings outside the main fence. In all cases occupied buildings should not be sited downwind of hazardous plant areas.