During production and transportation of hydrocarbon, especially in cases of extreme temperatures and pressures, it is possible that methane gas hydrates crystallize or asphaltenes precipitate in the pipeline. If not properly controlled, the hydrate crystals, asphaltene, or wax particles may precipitate and agglomerate to the point of plugging the pipeline. Removal of a hydrate or asphaltene plug in a subsea pipeline can be very expensive and dangerous. Hence, knowledge of fluid properties and operating conditions is critical to preventing formation and deposition of undesired solids. Flow assurance is an engineering analysis process of developing design and operating guidelines for the control of solids deposition such as hydrates, wax, and asphaltenes in subsea systems. Depending on the characteristics of the hydrocarbons fluids to be produced, corrosion, scale deposition, and erosion may also be considered in the flow assurance process.
In a nutshell, flow assurance consists of the design, strategies, and principles for ensuring that there is uninterrupted hydrocarbon production flowing from the reservoir to the point of sale.
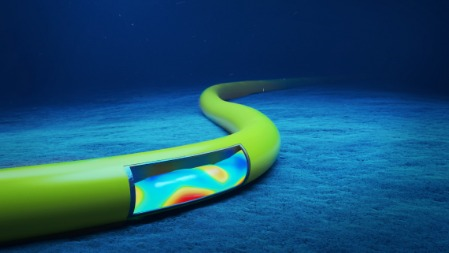
Aspects of the Flow Assurance Process
- Fluid characterization and flow property assessments.
The validity of the flow assurance process is dependent on careful analyses of samples from the wellbores. In the absence of samples, an analogous fluid, such as one from a nearby well in production, may be used. However, this entails significant risks because fluid properties may vary widely, even within the same reservoir. The key fluid analyses for the sampled fluid are PVT (Pressure Volume Temperature) properties such as phase composition, GOR (gas/oil ratio), and bubble point; wax properties such as cloud point, pour point; and asphaltene stability.
- Steady-state hydraulic and thermal performance analyses.
The steady-state flowline model can be generated with software such as PIPESIM or HYSYS. Steady-state modeling has several objectives:
- To determine the relationship between flow rate and pressure drop along the flowline. The flowline size is decided based on the maximum allowable flow rate and the minimum allowable flow rate.
- To check temperature and pressure distributions along flowlines in a steady-state condition to ensure that the flowline never enters the hydrate-forming region during steady-state operation.
- To choose an insulation combination that prevents the temperature at the riser base of a tie-back subsea system from falling below the minimum value for cooldown at the maximum range of production rates. The riser base temperature is determined as a function of flow rate and the combined wellbore/flowline insulation system.
- To determine the maximum flow rate in the system to ensure that arrival temperatures do not exceed any upper limits set by the separation and dehydration processes or by the equipment design.
- Transient flow hydraulic and thermal performance analyses.
Transient flowline system models can be constructed with software packages such as OLGA and ProFES. Transient flowline analyses generally include the following scenarios:
- Start-up and shutdown.
- Emergent interruptions.
- Blowdown and warm-up.
- Ramp up/down.
- Oil displacement.
- Pigging/slugging.
During these scenarios, fluid temperatures in the system must exceed the hydrate dissociation temperature corresponding to the pressure at every location; otherwise, a combination of an insulated pipeline and the injection of chemical inhibitors into the fluid must be simulated in the transient processes to prevent hydrate formation.
At PetroPlat we render Flow Assurance Service to both Brownfield and Greenfield plants/facilities.
In Greenfield operations, if there is no proper viability study of a potential discovery, particularly in a Deepwater site, the flow of hydrocarbon can remain uncertain until it’s too late to prevent recurrent issues. Our properly integrated flow assurance plan includes a full risk assessment, which covers:
- The modelling of multiphase flows and temperature changes.
- The projection of hydrate, wax, asphaltene, scale, and emulsion formation.
- The interface with other operational processes.