To determine SIL Levels of process hazards, it is helpful to understand the Safety Life Cycle.
The IEC standards define a concept known as the Safety Life Cycle, see figure below. The Safety Life Cycle provides a repeatable framework whereby all process hazards are identified and analysed to understand which hazards require the use of a SIS for mitigation. By design, this is a cyclic process, not a linear process with an endpoint. Any changes in process design, operating conditions, or equipment requires cycling back to the beginning to ensure any changes are properly implemented.
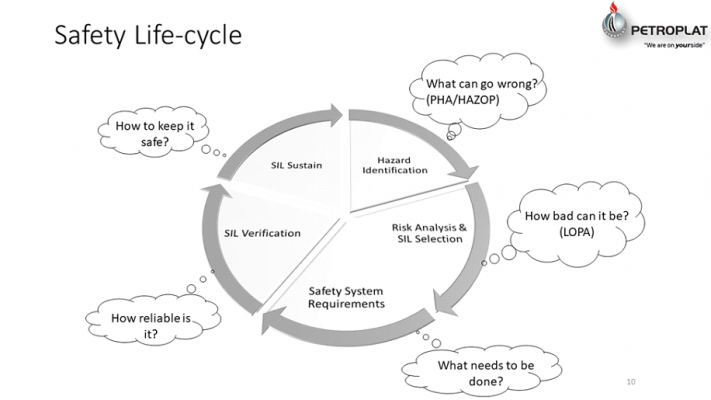
Safety Integrity Level: or SIL Verification demonstrates the capability of a Safety Instrumented Function (SIF) in accordance with IEC 61508 and IEC 61511 against the following requirements:
⦁ Quantifying the effect of random hardware failures (Probability of Failure on Demand (PFD) or the Average Frequency of Dangerous Failures (PFH));
⦁ Hardware safety integrity architectural constraints (Safe Failure Fraction (SFF), Hardware Fault Tolerance (HFT), Element Type A or B).
⦁ Systematic capability.
⦁ Common Cause Failure (CCF).
Definitions
Safety Integrity Level (SIL): SIL is a measurement of safety performance required for a safety instrumented function.
Safety Instrumented Function (SIF): Combination of sensor, logic solver and final element that detects a single hazard and act to bring the process to a safe state.
Examples of SIFs
⦁ On detecting high pressure, prevent vessel rupture by opening valve to relief system.
⦁ On detecting high temperature, prevent column rupture by shutting off steam flow to the re-boiler.
⦁ On detecting high level, open drain valve to direct excess liquid to sump to reduce environmental damage.
⦁ On detecting high level, close a feed valve to prevent tank overflow.
⦁ Stop motor by disconnecting power or activating brake when severely high speed is detected.
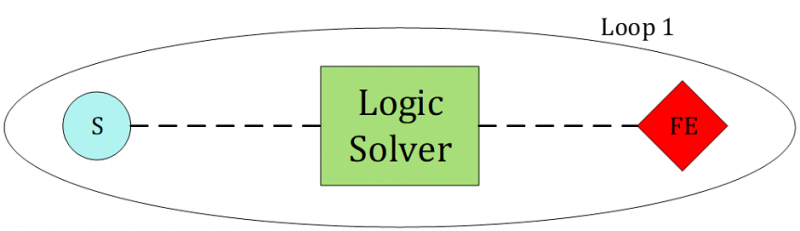
Safety Instrumented Functions (SIF) used Safety Instrumented System SIS to implement one or more safety instrumented functions. It is installed to automatically take an industrial process to a “safe state” when predetermined specified conditions have been violated.
Levels for Specifying the Safety Performance Targets for Safety Instrumented Function (SIF).
There are four discrete levels (1 to 4) for specifying the safety performance targets for safety instrumented function.
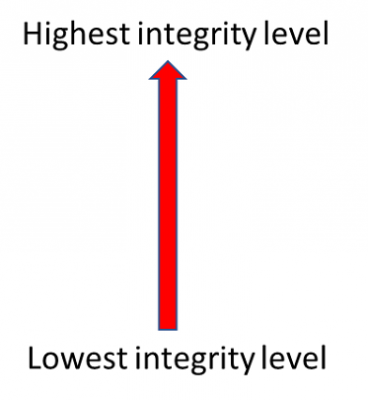
The SIL level number is based on the amount of risk reduction needed to maintain an acceptable level of risk.
A higher SIL level means a greater process hazard and a higher level of protection (risk reduction) is required from the SIF.
Steps for SIL Determination
In summary, the SIL Determination steps involves:
⦁ Identify the consequence to screen the scenarios.
⦁ Identify the company’s tolerable frequency for the consequence.
⦁ Identify the initiating event of the scenario and determine its frequency (i.e., the initiating event frequency).
⦁ Identify the Independent Protection Layers (IPLs) and assign the probability of failure on demand (PFD) for each IPL.
⦁ Calculate the mitigated event frequency by taking the product of the initiating event frequency, the IPL PFDs and if applicable, the probability of enabling event and the probability of conditional modifier.
⦁ Compare the mitigated event frequency to the criteria for tolerable frequency for the company.
⦁ If the risk criteria are not met, the remaining risk gap will be filled by the installation of a Safety Instrumented Function (SIF). The size of the risk gap determines the Safety Integrity Level (SIL) of the SIF required.
Target SIL
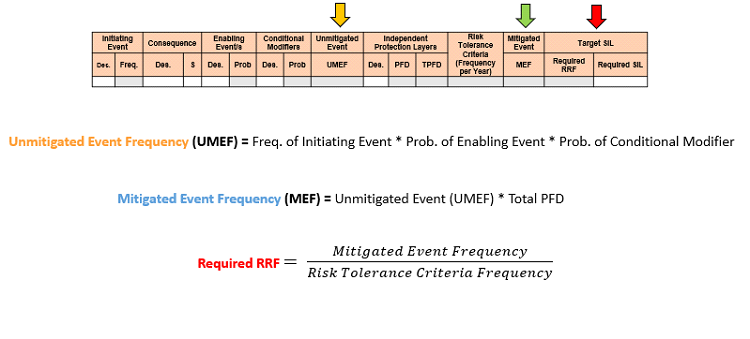