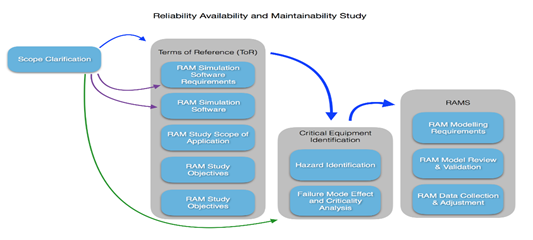
Global competition necessitates automated production systems that are seamless, efficient, and of high quality. Sudden production machine failures can be costly in an automated system with multi-stage and fast manufacturing processes.
Failure of equipment to work as required is a common cause of manufacturing machine breakdowns. This adds to waste in the manufacturing process, such as waiting for unplanned downtime or product rejections. As a result, detailed reliability knowledge is critical in estimating unplanned downtime costs and spare parts, as well as recommending the best maintenance intervals. The implementation of a good reliability program will ensure the collection of important data about the system’s reliability performance all the way through the operation stage and will direct the use of this data in the employment of appropriate analytical techniques and management processes.
RAM analysis can be conducted at various stages of the life cycle of the project based on the availability of data. Pre-FEED, FEED, and Detail Engineering at any stage. But during every stage, the level of details and depth differs.
- Pre-FEED (i.e., design conceptualization) – RAM analysis can be used to compare various design options that are being considered through quantification of the production output of each option. Conducting a RAM analysis at this stage, whilst the design is still being finalized is known to reduce the cost and schedule impact on the project than if conducted at a later stage.
- FEED – At the FEED stage, when critical equipment is being identified which could cause significant production losses. A RAM analysis would normally be conducted to optimize the equipment configuration and identify the requirements of any further spares or equipment redundancies to optimize the availability of the system.
- Detailed Engineering – At the detailed engineering stage it is likely that the design is frozen with minimal changes. A RAM study at this point would help in identifying performance targets that must be met by the equipment, which can be used as part of the equipment design specification during procurement.
The complex of RAM factors constitutes a strategic approach for integrating reliability, availability, and maintainability, by using methods, tools, and engineering techniques (Mean Time to Failure, Equipment down Time and System Availability values) to identify and quantify equipment and system failures that prevent the achievement of the productive objectives. The application of such methodologies requires a deep experience and know-how together with the possibility of acquiring and processing data in operating conditions.
Objectives of a RAM Analysis
Our skilled team of consultants have been proving Reliability, Availability and Maintenance studies and analysis for various industries. The major goals of a RAM analysis are for it to be used as a decision-making tool to raise the system’s availability, and thus boost the overall profit as well as reducing the life cycle costs (inclusive of the cost of maintenance, lost production, operating etc.). RAM analysis can be performed on systems and facilities of different types and sizes in various industries ranging from oil and gas, water, and wastewater treatment, nuclear, process, manufacturing, and lots more.
Inputs required to conduct RAM analysis:
As a minimum the following information would be required in order to conduct the analysis:
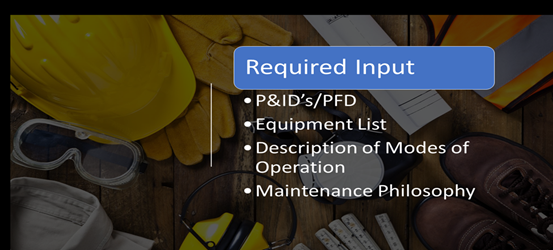
Based on the project requirements, additional information may be required like production profiles, operations historical data etc.
RAM Methodology
The figure below provides an overview of RAM methodology

Results of RAM Analysis:
The benefits of undertaking RAM Studies include:
- A reduction in the maintenance and sparing costs, while maintaining and/or increasing production levels.
- A decrease in the duration of any unplanned and planned outages.
- Optimization on capital investment by reducing the cost of production.
- Optimization of capital improvement options at the plant and enterprise levels when improve budgets are constrained.
- Accurate forecasts of equipment lifecycle costs that reflect the equipment age, duty cycle, and maintenance effectiveness.