What is HAZOP
A HAZOP is a systematic assessment tool used to identify and address potential hazards in industrial processes before an incident occurs that could affect the Safety of people or assets while hindering Productivity. HAZOP studies are typically performed while new facilities are being designed and constructed when new processes are added or when processes change. Most regulatory agencies also require periodic HAZOP studies on existing processes.
The HAZOP assessment is typically performed by a small team that breaks each step of a process down for individual review to identify potential deviations from the original process design. Like all PHAs, HAZOPs go beyond the review of how a process is supposed to operate to identify unintended outcomes and explore their potential ripple effects on health and safety.
Objective
To assess the hazard potential of mal-operation or malfunction of equipment and the consequent effects on the facility.
Methodology
As HAZOP undertakes the careful review of complex processes involved in the handling and processing of chemicals and materials that can potentially harm workers and stakeholders if not properly contained and handled, it is important to follow the following steps:
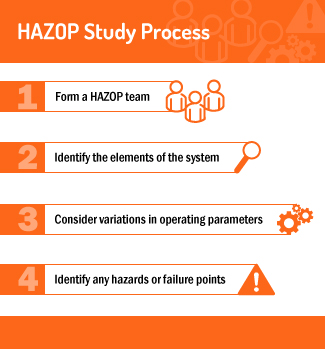
A multidisciplinary HAZOP team composed of a team leader and members who can collaborate and provide different perspectives based on their fields of expertise at realizing sources of risks and possible deviations from design.
- Identify processes, P&ID, and HAZOP nodes
When beginning a HAZOP study, it is important to identify the processes in operations, be familiar with the process/piping and instrumentation diagram (P&ID) and be aware of all the nodes.
P&ID are drawings or diagrams that provide the visual representation of interconnected processes, equipment, and controls in the physical plant. HAZOP nodes are sections in the entire process where changes happen, and they need to be reviewed along with Material Safety Data Sheets (MSDS) so that parameters can be defined, and deviations are identified. Parameters or safe operating limits are defined during the review of nodes so that deviations can be determined, and guide words are selected.
- Control Identification and Safety Monitoring
With hazards identified, the corresponding hazard mitigation or elimination strategies shall then be applied to maintain the safety of the workplace. With ongoing processes and production, monitoring should also be established to ensure that safeguards are still effective and safety procedures are being followed.
Results from HAZOP analyses can be used to help elevate safety within a plant and improvements in safety practices and processes. It shall be appropriately communicated to employees e.g., occupational safety, chemical safety, and hygiene safety processes.
An effective approach to safety training or program will also help hasten the implementation of changes and reinforce safety across the board.